The whole process sounds easy, but behind the scenes there are a lot more things happening.
- Internal fruit quality is checked continuously.
- Packing materials needs to be ordered, received, and checked.
- We need to make sure that the Carton folding team are keeping up, so that the packers always have the correct carton.
- Bins that arrive at the Packhouse needs to be inspected according to PPECB rules and regulations. This is to ensure that no decease and/or insect is present in or on the fruit that is prohibited for export to other countries.
- Carton labels must be printed and supplied to the packers during the day.
- Paperwork, and more paperwork to make sure that there is a trail of where the fruit came for as well as the documents needed for PPECB inspection and export.
- Transport bookings must be organized, and trucks need to be loaded.
- We need to ensure that the packing line is run smoothly and that all products used in the line is used at the correct concentrations.
- The cleaning team is cleaning and sanitizing the whole day.
- Packing programs must be worked out, and the progress on orders monitored during the day.
- Visitors need to be shown around, and partners need attention as well. Visitors are always welcome at the Packhouse but needs to follow the Packhouse rules.
- Fruit that is not send to export markets, are sold either to the public in bulk or sent to the juicing factory.
- And so much more ………
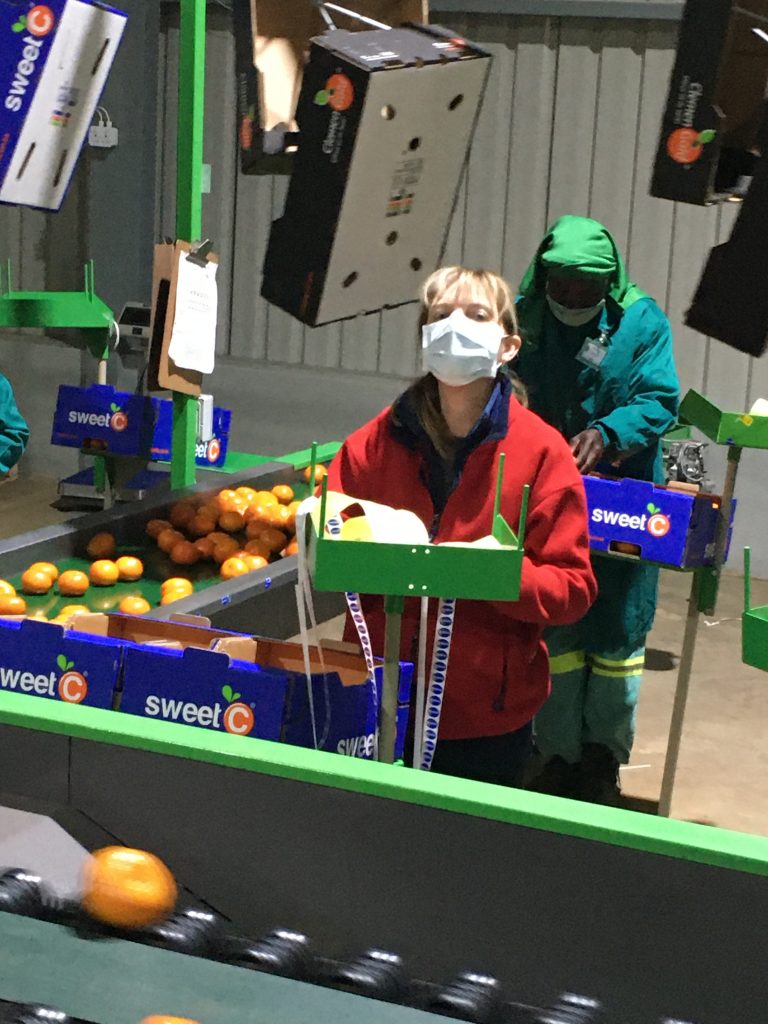
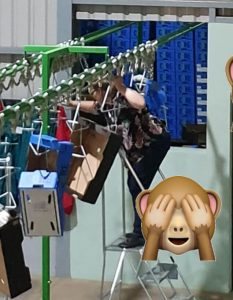